
Cable Protection, Safety & Performance for Heavy Vehicles
Around the world, millions of commercial vehicles and farm and heavy-duty equipment travel billions of miles each year. These types of vehicles often operate in the toughest conditions and harshest environments. Some vehicles are in service for long hours or travel across treacherous terrain, putting strain on the vehicle’s electrical wiring in addition to the damaging impacts of vibration, corrosion and regular power jet washing.
A vehicle’s electrical wiring is its heartbeat and helps drive its performance, productivity, and reliability, all of which impact its cost of ownership. It's crucial that a vehicle is safely protected. Without correct and reliable harness protection, commercial and heavy-duty vehicles can be vulnerable to downtime and more frequent, costly repairs.
Focusing on a diverse range of commercial and heavy-duty vehicles, the ABB Harnessflex® team works closely with many original equipment manufacturers (OEMs) and heavy-duty vehicle engineers to develop cable management and protection solutions for electrical connectors and systems — a critical area of a vehicle’s engine wiring harness. Harnessflex is a leading designer and manufacturer of flexible conduit systems and connector interfaces that protect critical electrical wiring in the automotive industry, including chassis and engine manufacturers within bus, agricultural, and heavy-duty vehicle markets.
Maximizing lifespan and performance
ABB offers solutions that can help:
- Protect commercial & HDV investments
- Enhance safety & reliability
- Improve equipment performance
- Extend the life of the vehicle
- Lower emissions & meet or exceed evolving requirements
- Reduce installation & maintenance
Contact IEWC Engineered Services
Harnessflex and IEWC's teams of engineers stand ready to help you spec out the HFX products you need for you project.
With an understanding of OEM and harness-maker requirements, ABB’s Harnessflex® team produces an extensive line of products and bespoke designs that easily integrate into the wiring harness of commercial and HDVs. As a result, Harnessflex® has developed a wide range of durable and protective backshells for commonly used electrical connectors, cable management solutions, cable glands, vibration friendly profile conduit, and fittings that help defend effectively against high pressure wash-down, excessive cable strain, corrosion, and mechanical abrasion. These include standard low voltage systems, including those exposed to the temperature extremes of modern diesel engines, as well as high voltage, clean power systems such as hydrogen and battery systems.
Environmental Consideration
Whether it’s a fire truck that maneuvers through traffic in response to an emergency, a delivery vehicle in constant use, or logging equipment that travels extreme terrain, the protection needs to match the application and working environment. It's vitally important that vehicle wiring harnesses are able to withstand intense strain when operating in the field. With an intuitive, practical design and proven strength when subjected to intense testing, the Harnessflex® Heavy Duty Series offers safer and more secure cable protection by providing a continuous sturdy link between harness and connector. The series is designed for use with all TE HDSCS and Aptiv CTCS XP Type B & E connectors, helping maintain continuous vehicle operation even in the toughest operating conditions.
As an integrated solution, Harnessflex® conduits, fittings and accessories are designed to be used as a combined system and are extensively tested in several ways:
- Compression & crush
- Tensile & pull off
- Ingress protection (jet wash safe)
- Oil & chemical resistance
- UV resistance
- Extreme cold & hot temperatures
- Vibration & abrasion
- Protection from dust, debris & paint with Harnessflex® connector shields
This robust testing helps Harnessflex® complete system solutions provide dependable routing and protection of electrical wiring against damage by impact, mechanical abrasion, liquid ingress, corrosive salts and chemicals, and extreme temperatures.
Assembly, Installation & Maintenance Processes
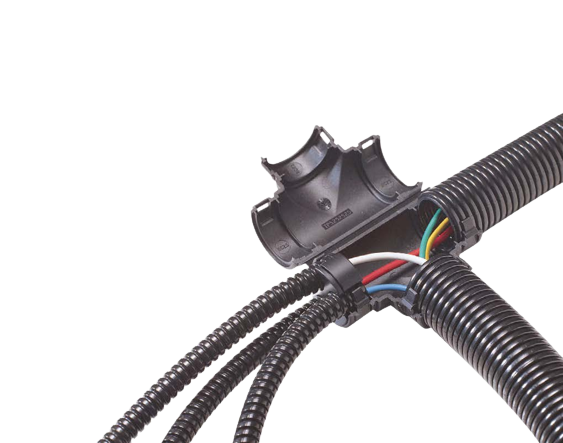
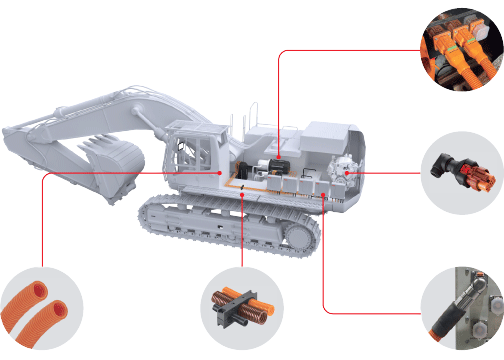
For the harness-maker, the labor involved in assembling the harness is an important consideration. If parts are difficult to put together, this adds to the installation time and ultimately overall costs. When the competitor backshell for TE connectors was tested for ease of assembly, clips were found to be hard to open with a screwdriver, causing parts to slip and creating potential risk of hand injuries. With bigger overall dimensions than the Harnessflex® Heavy Duty Series, the bulky and square design of the other backshell and protruding clips take up valuable space in the engine compartment. Although the connector plug sits inside the backshell, there is no retaining clip for the conduit, which falls out easily and makes assembly tedious. Without being held firmly in place by hand, components could drop out and disrupt installation, cause damage, and increase both assembly time and cost.
By comparison, the Harnessflex® Heavy Duty Series is easy to open with a screwdriver and the backshell is a hinged, one-piece design that smoothly closes around and captures any parts, helping to make Harnessflex® assembly operations fast and easy. The tightly constructed backshell is also ideal for engine harness, providing wire protection without taking up valuable engine space.
Footprint
While space is already limited inside a vehicle, some engine types have tighter constraints and more complex control systems. For example, hydrogen engines have a smaller footprint and require connector protection with increased strain relief. Harnessflex® has developed smaller wiring harnesses to fit these compact footprints and a range of systems, applications and environments.
In addition to analyzing the above factors, cost and frequency of replacement are important considerations. As standard, Harnessflex® conduit systems carry a 5-year warranty, with some customers having reported Harnessflex installations that have been in service since the 1980s. Importantly, based on previous testing results, Harnessflex conduit systems provide 10 to 150% greater life expectancy in dynamic or vibrating applications when compared with other products.